Previous slide
Next slide
“When there’s no time for downtime.”
OUR PARTNERS:
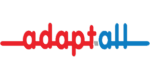
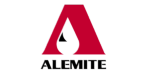
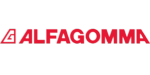
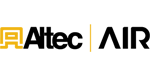
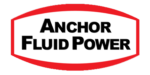
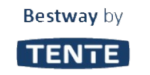
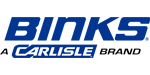
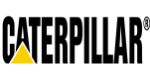
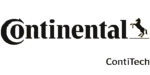
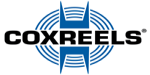
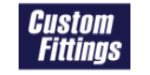
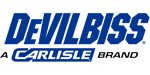
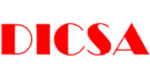
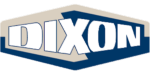
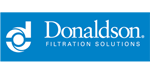
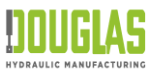
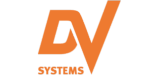
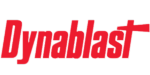
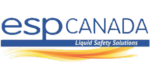
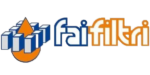
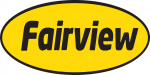
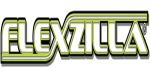
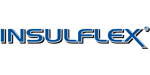
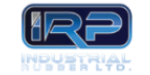
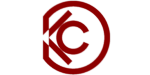
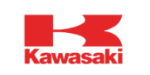
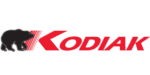
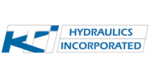
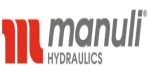
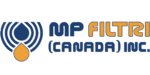
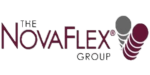
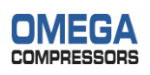
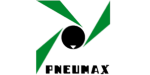
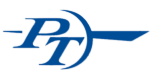
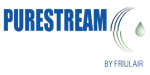
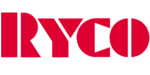

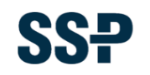
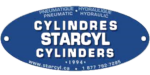
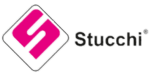
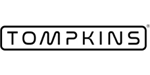
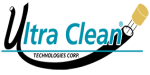
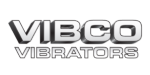
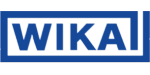
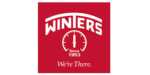
About Us
We know that downtime costs you money.
At Seaway Fluid Power we know that downtime costs you money. Getting you back up and running as quickly as possible is the focus of everything we do.If you need a part, we carry an extensive parts inventory. This means we can get you back up and running without having to wait for parts to arrive. It also means we have a wide enough variety of parts that we can put together a complete end-to-end solution to address your needs in one spot – quickly.
If you need more than just parts, then we have the experience and knowledge in-house to create innovative solutions to your most demanding repair and new fabrication challenges.
Our Customers speak for us
4.8/5
“Awesome guys, always have what I need, they know their stuff, I’ll be a long time customer”
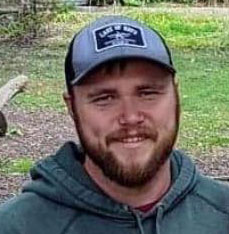
Chris M.
4.8/5
“Great service and great people to deal with.”
Kellie M.
4.8/5
“I highly recommend the services and products Seaway Fluid Power offer."
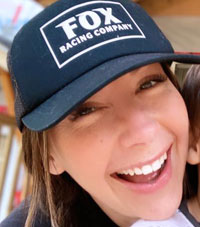
Carolyn C.